Оптическая система, методы визирования и электроника
Экспериментальное определение коэффициента излучения
В справочных таблицах можно найти значения коэффициентов излучения для различных материалов, взятые из технической литературы и полученные в результате измерений. Существуют различные способы определения коэффициента излучения
Способ 1: С помощью термопары Одновременно с бесконтактным измерением температуры выполняется дополнительное измерение с помощью контактного датчика (термопары), которое позволяет получить реальную температуру поверхности объекта. После этого необходимо скорректировать коэффициент излучения на инфракрасном термометре таким образом, чтобы отображаемое значение температуры соответствовало значению, полученному с помощью контактного измерения. Контактный датчик должен иметь хороший тепловой контакт и низкий уровень теплоотдачи.
Способ 2: Имитация черного тела с помощью контрольного объекта из измеряемого материала Отверстие (глубиной ? 1/3) в теплопроводящем материале ведет себя так же как черное тело с коэффициентом излучения близким к 1. Из-за особенностей оптической системы инфракрасного прибора и расстояния, с которого выполняются измерения, необходимо нацеливаться на дно отверстия. Измерив действительное значение температуры на отверстии, можно определить коэффициент излучения.
Способ 3: Использование известного опорного коэффициента излучения Пластырь, изолента или краска с известным коэффициентом излучения, нанесенные на поверхность объекта, позволяют выполнить опорные измерения. Установив известный коэффициент излучения на инфракрасном термометре можно получить температуру пластыря, ленты или краски. После этого измерьте температуру поверхности, находящейся рядом рядом, одновременно изменяя коэффициент излучения таким образом, чтобы термометр показывал такую же температуру. Теперь на приборе будет установлено правильное значение коэффициента излучения.
Конструкция инфракрасных термометров
Инфракрасные термометры имеют различные характеристики и конструкцию, используют разные оптические системы, электронную начинку, технологию, размеры и корпусы. Тем не менее, способ обработки сигналов у них одинаковый: всё всегда начинается с измерения потока инфракрасного излучения и заканчивается электронным выходным сигналом температуры.
Оптическая система и окна
Оптическая система – обычно использующая линзовую оптику – стоит в начале измерительной цепочки. Поток инфракрасного излучения, испускаемый измеряемым объектом, проходит через линзу и фокусируется на приемнике излучения. Измерения с использованием излучения будут правильными, только если измеряемый объект имеет размеры больше измеряемого прибором пятна. Оптическое разрешение прибора показывает размер измеряемого пятна с определенного расстояния. Оптическое разрешение - это отношение расстояния до измеряемого объекта к диаметру измеряемого пятна (D:S). Чем выше это значение, тем лучше оптическое разрешение.
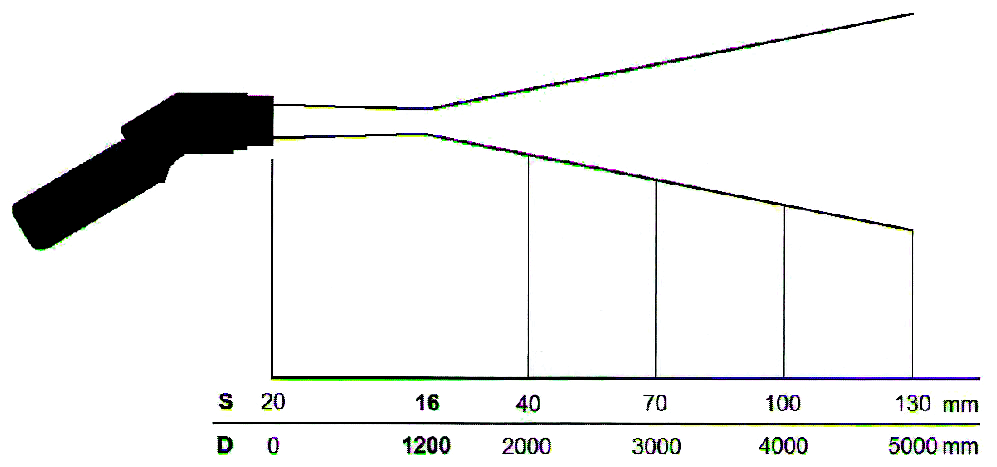
Оптическая схема инфракрасного измерительного прибора
Из-за пропускания материала инфракрасной линзы, оптическая система может использоваться только в определенном диапазоне длин волн. На рисунке показаны графики поведения различных типичных материалов, используемых для изготовления линз и окон с указанием соответствующей длины волны для инфракрасных термометров.
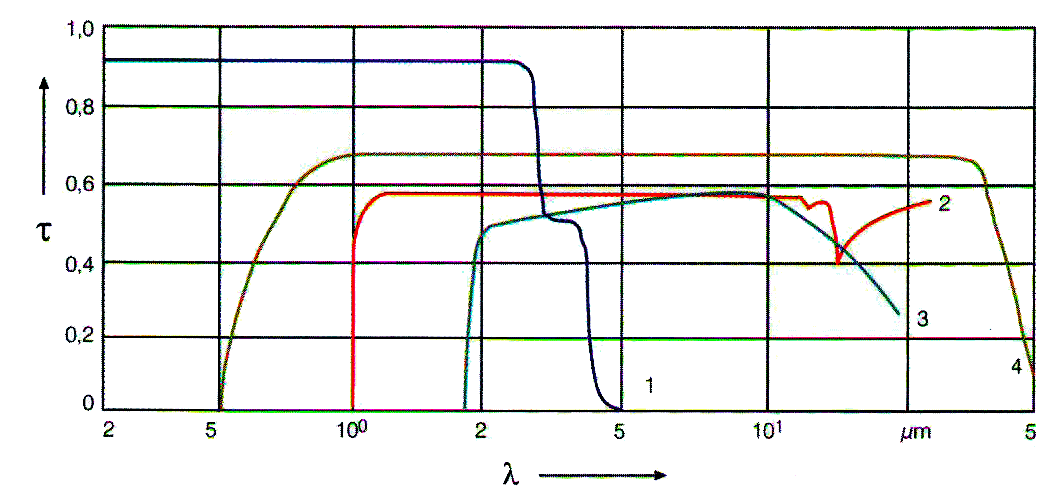
Коэффициент пропускания типичных инфракрасных материалов (толщина 1 мм) 1 Стекло, 2 Германий, 3 Аморфный кремний, 4 KRS5
Для некоторых видов измерения температуры необходимо использовать инфракрасные окна, например, при измерении в закрытых лабораторных колбах, печах или вакуумных камерах. Коэффициент пропускания измерительного окна должен соответствовать спектральной чувствительности прибора. Плавленый (кристаллический) кварц подходит для измерения высоких температур. Для измерения низких температур в спектральном диапазоне 8-14 мкм можно использовать такие специальные материалы, как германий, AMTIR или селенид цинка. Кроме того, для выбора правильного материала окна важную роль играет его диаметр, температурные условия и максимально допустимое давление на линзу. Толщина окна диаметром 25 мм, которое бы выдерживало давление в одну атмосферу, должна составлять 1,7 мм. Материал окна, который к тому же является прозрачным в видимом диапазоне, позволяет выполнять точное наведение датчика на измеряемый объект (например, внутри вакуумной камеры).
Сравнительная таблица материалов окон
Материал окна |
Al2O3 |
SiO2 |
CaF2 |
BaF2 |
AMTIR |
ZnS |
Рекомендуемый спектральный диапазон, в мкм |
1…4 |
1…2,5 |
2…8 |
2…8 |
3…14 |
2…14 |
Макс. температура окна, °С |
1800 |
900 |
600 |
500 |
300 |
250 |
Пропускание в видимой области спектра |
Да |
Да |
Да |
Да |
Нет |
Да |
Устойчивость к воздействию влажности, кислот, аммиачных соединений |
Очень хорошая |
Очень хорошая |
Слабая |
Слабая |
Хорошая |
Хорошая |
Пропускание окон с просветляющим покрытием значительно выше (до 95%). Потери на пропускание можно скорректировать при помощи подстройки коэффициента пропускания, если производитель указал значение, соответствующее диапазону длин волн. Если же нет, его необходимо определить с помощью инфракрасного термометра и эталонного источника излучения.
Последние достижения в системах визирования
Новые принципы измерения и методы визирования облегчают работу с инфракрасными термометрами. Достижения в разработке полупроводниковых лазеров позволяют использовать многолучевые лазерные системы для указания размеров измеряемого пятна. Таким образом, реальные размеры измеряемого пятна на измеряемом объекте можно обозначить при помощи перекрестия лазерных лучей. В некоторых приборах вместо оптических систем наведения используются видеокамеры.
Разработка высокопроизводительной оптической системы с лазерным наведением
В простых недорогих портативных инфракрасных термометрах используются одноточечные лазерные целеуказатели, которые обозначают центр измеряемого пятна с параллаксом по умолчанию. Поэтому пользователям приходится определять размеры измеряемого пятна с помощью оптической диаграммы. Если измеряемый объект занимает только часть измеряемого пятна, повышение температуры будет отображаться только в виде среднего значения температуры горячего участка и холодных окружающих объектов. Повышенное сопротивление электрического соединения вследствие поврежденного коррозией контакта приводит к перегреву. Из-за маленьких размеров объекта и слишком больших размеров измеряемого пятна такое повышение температуры будет выглядеть как незначительный перегрев, что может привести к несвоевременному выявлению потенциально опасных перегретых участков. Чтобы показать реальные размеры измеряемого пятна, были разработаны оптические системы визирования с обозначением его размеров. Они позволяют выполнять точное наведение прибора на объект. Так как лазерные пирометры значительно легче и безопаснее контактных термометров, инженеры попытались создать систему обозначения размеров измеряемого пятна с помощью лазерного указателя, независящую от расстояния – в соответствии с отношением «расстояние : размер пятна», показанным на диаграмме.
Два перекрещивающихся лазерных луча приблизительно показывают уменьшение измеряемой области и ее увеличение на больших расстояниях. Диаметр измеряемого пятна обозначается двумя точками на внешней окружности пятна. Из-за конструктивной особенности угловое положение этих точек лазера на окружности изменяется, что затрудняет процесс наведения.
Использование перекрестия
Новые способы построения систем визирования позволяют обозначать измеряемое пятно инфракрасного термометра в виде перекрестия реального размера, которое точно соответствует размерам измеряемого пятна.
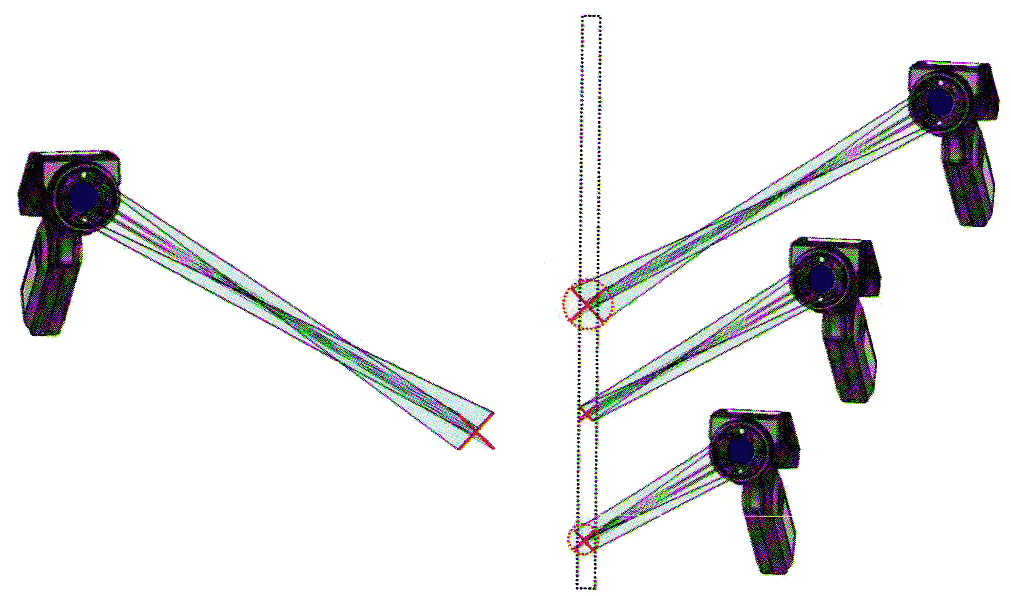
Инфракрасный термометр с лазерным перекрестьем для точного определения размеров измеряемого пятна
Четыре лазерных диода расположены симметрично по кругу инфракрасного оптического измерительного канала. Они установлены на устройствах формирования линий, которые создают линию определенной длины в пределах фокусного расстояния. Устройства формирования линий расположены попарно и направлены друг на друга. Они производят наложение проецируемых лазерных лучей в точке фокуса. Таким образом, образуется перекрестие, которое точно показывает диаметр измеряемого пятна. При увеличении или уменьшении расстояния происходит частичное наложение, из-за чего пользователь получает изменение длины линий и соответственно изменение величины перекрестия. При помощи такой технологии можно с первого раза определить точные размеры измеряемого пятна. Эта разработка повышает уровень практического использования приборов с хорошими оптическими характеристиками.
Переключение в режим короткого фокуса
Обычное применение приборов для обслуживания электроники и проверки качества в промышленности предполагает оптимальное расстояние измерения приблизительно 0,75…2,5 м. Кроме этого, часто бывает необходимо измерять небольшие объекты на маленьких расстояниях. Поэтому инженеры разработали изделия, которые позволяют осуществлять фокусировку в определенных пределах. Однако им еще не удалось получить измеряемое пятно диаметром меньше 1 мм. |